What is the role of galvanized hydraulic connectors? The most common surface treatment technology in our hydraulic system is galvanization, which makes our hydraulic products look more beautiful and makes hydraulic connectors more corrosion-resistant during use.
Per esempio, IL 10143-8-8, 10643-6-6 and other hydraulic connectors we most commonly see in construction machinery systems are galvanized. Galvanization is a surface treatment technology that coats the surface of metal products, alloy products or other materials with a layer of zinc metal for aesthetics and anti-rust effects.
Zinc is a metal with high corrosion resistance. It can isolate iron and other metals from air or water, so that rust-prone metals such as iron cannot undergo the chemical reactions required for rust. In the process of galvanizing, zinc and iron react chemically to form a series of alloys, so that the zinc layer and iron are closely combined. Since the zinc layer is firmly combined with the underlying steel material, the coating will not be damaged even if the galvanized steel object undergoes operations such as rolling, disegno, bending, eccetera. to change the shape
Electrochemically, zinc is more active than iron. COSÌ, even if the zinc layer that coats the iron breaks down and the iron is exposed to the air, the remaining zinc still provides sacrificial protection to the iron against rust.
Il ruolo della zincatura dei connettori idraulici.
Our common galvanizing methods mainly include hot dip galvanizing (HDG), electro galvanizing (EG) and cold galvanizing.
Hot dip galvanizing (HDG)
Hot-dip galvanizing (HDG) is one of the common galvanizing methods in which iron or steel is completely immersed in molten zinc. The benefit of hot-dip galvanizing is the relatively low cost compared to electro-galvanizing
Chemical reactions during galvanizing will only occur on clean iron or steel surfaces. Perciò, before hot dipping, steel materials will be degreased (remove oil stains with alkaline chemicals), washed repeatedly, and pickled to ensure the quality of the finished product. Afterwards, the iron and steel material is immersed in a flux ( the main components are usually ammonium chloride and zinc chloride) and dried to preheat. After the iron and steel material is processed, the iron and steel material will be immersed in molten zinc liquid (that is, molten zinc). A series of complex chemical reactions will occur between iron and zinc to produce iron-zinc metal compounds, and a zinc layer will be formed on the iron surface. The the zinc layer is 6 to 20 microns in thickness, relatively thick, usually composed of pure zinc layer and alloy layer. The process after hot dipping includes cooling, passivation, testing, eccetera.
The properties of the zinc layer can be adjusted by adding other metals into the molten zinc solution: for example, adding metals such as aluminum, magnesium, and nickel can improve the corrosion resistance of the zinc layer, and adding metals such as aluminum, lead, tin, and antimony can optimize the zinc layer’s appearance
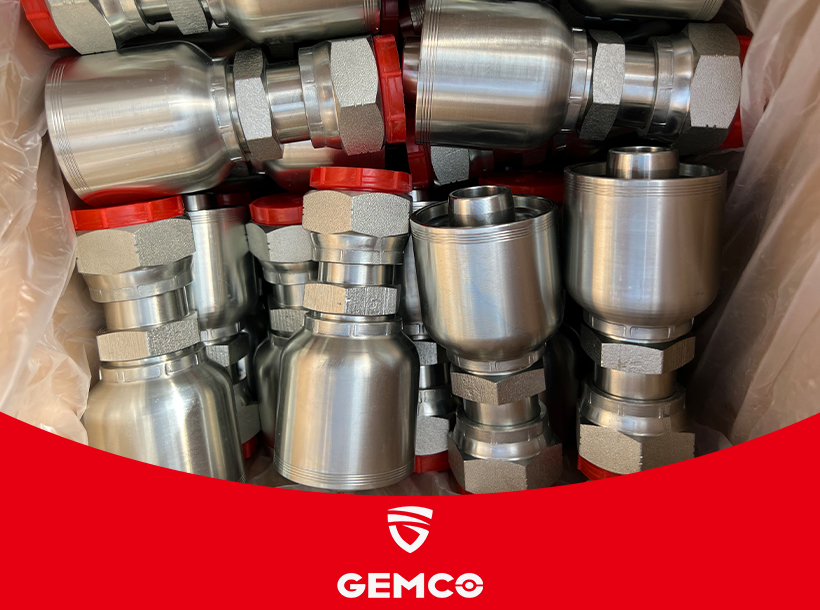
raccordo idraulico
Electro galvanizing (EG)
Electrogalvanizing (EG) is a type of electroplating and its production line is very expensive; Compared with hot-dip galvanizing, the advantage of electrogalvanizing is that the zinc layer is more even. In the process of electro-galvanizing, the iron or steel that needs to be galvanized is the cathode, and the zinc to be plated is the anode, with the zinc salt solution as the electrolyte
Cold galvanizing
Cold galvanizing refers to the coating of zinc-rich paint on the surface of steel materials. This method only requires the equipment used for painting. Tuttavia, the zinc layer (known as a zinc-rich coating) is less durable and offers less sacrificial protection to iron and steel materials.
Perciò, the most common surface treatment technology for our common one-pieces, adattatori, innesti rapidi, E high-pressure ball valves is galvanization. Most of Gemco’s hydraulic products also use this technology to carry out surface treatment on our hydraulic products. This technology can effectively help the products against rust, so that our hydraulic products remain corrosion-free and leakage-free during long-term use, which increases its service life.